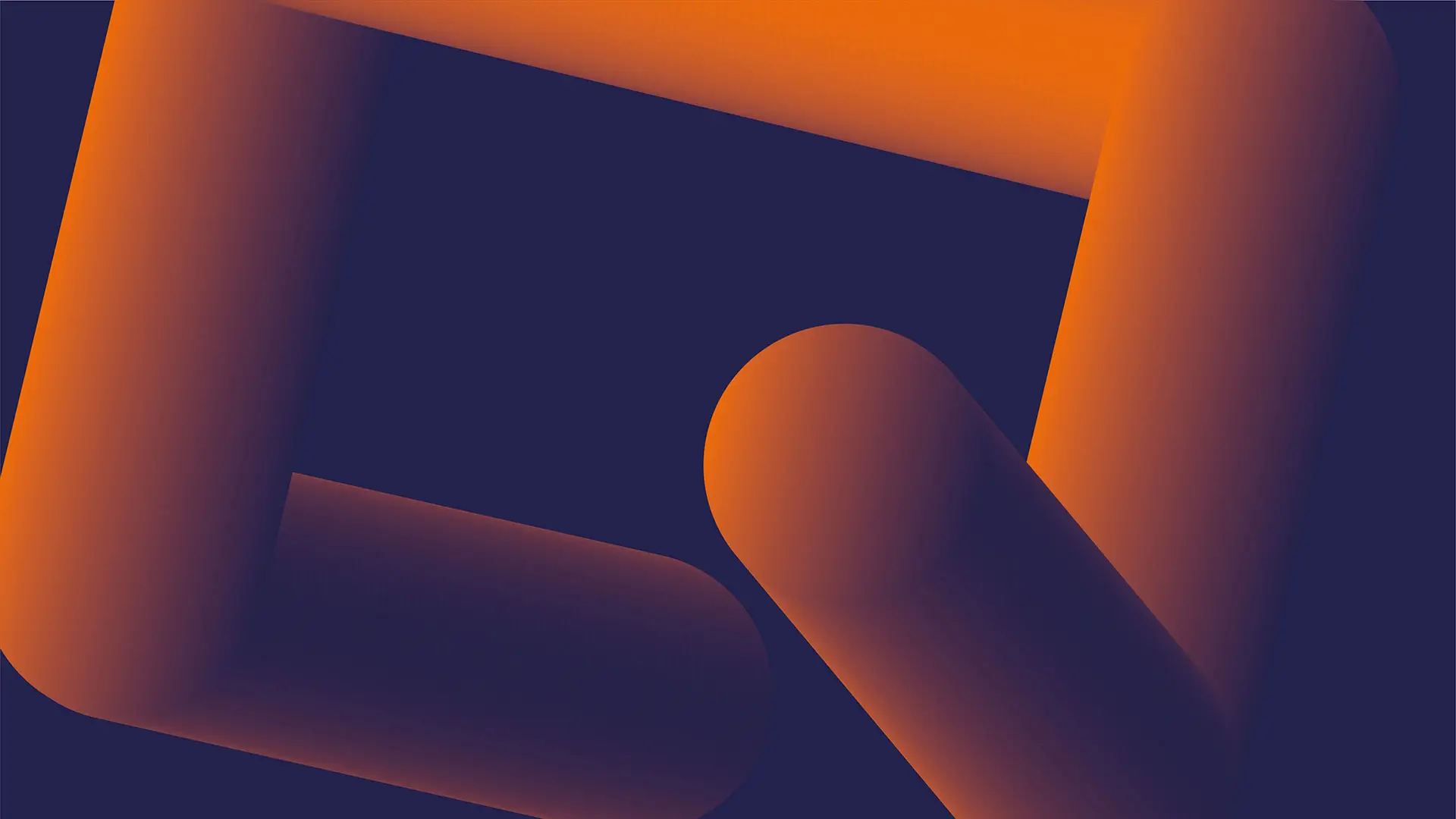
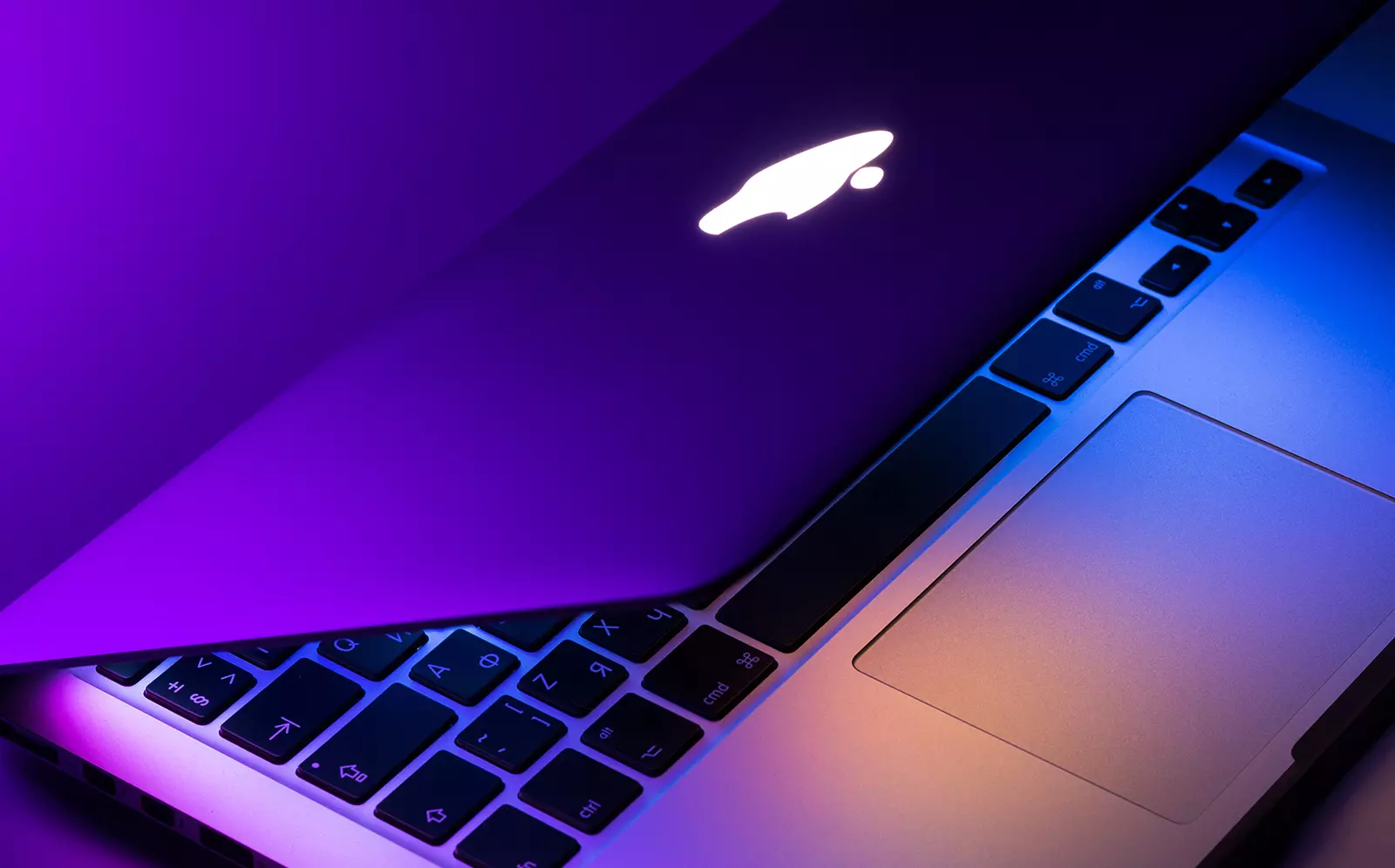
Q-Pall: driven by sustainability
Every company faces sustainable challenges: reducing production costs, using fewer raw materials, and offering sustainable products. Q-Pall shares these ambitions and translates them into concrete actions within our Orange Values — a nod to our Dutch identity and our commitment to responsible business practices.
By controlling the entire chain — from production and distribution to sales — we can offer unique technical and logistical conditions that contribute to efficient and sustainable business operations for our customers.
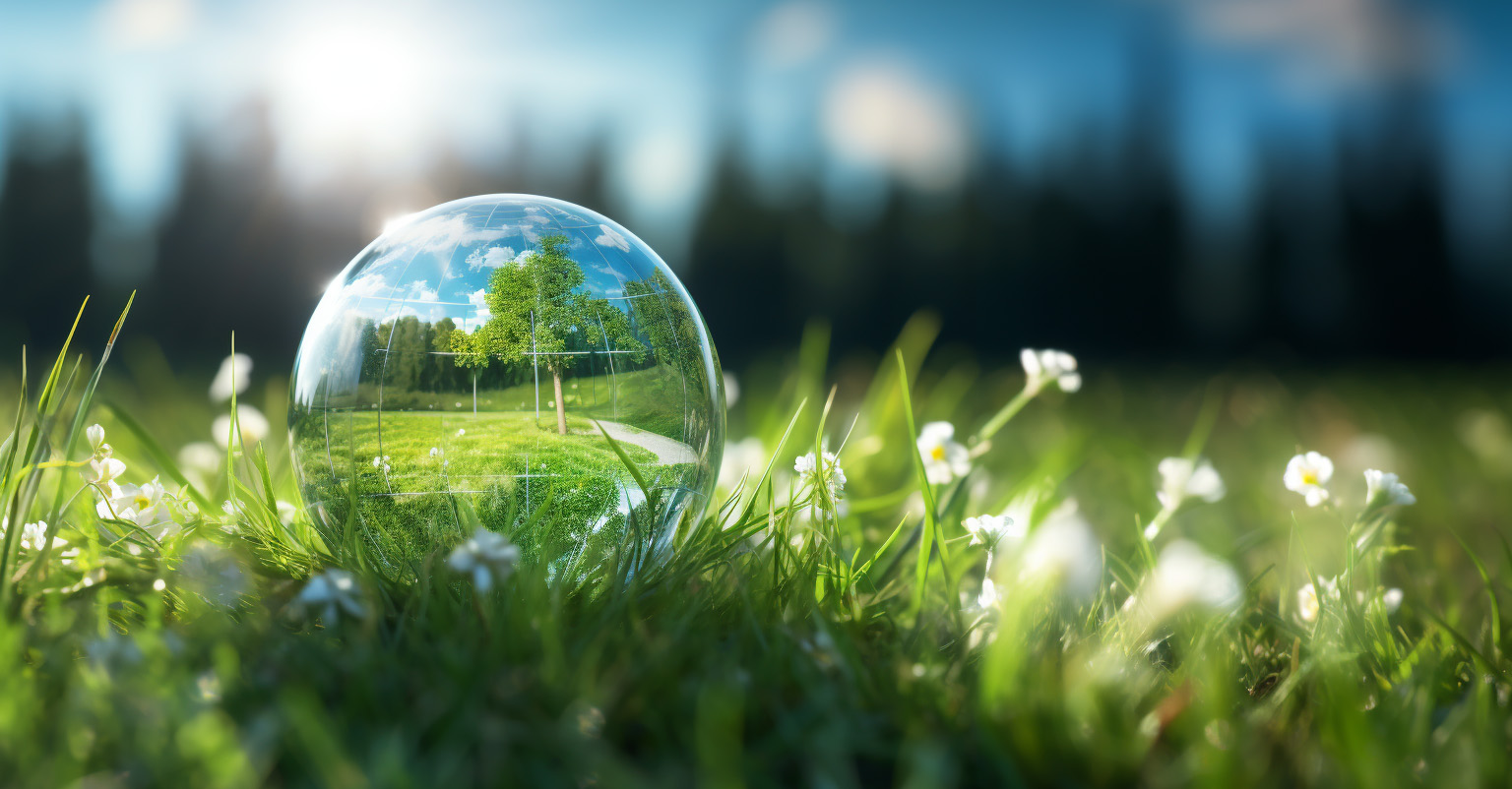
CO2 reduction
The emission of CO2 gases directly contributes to climate change, leading to global warming and rising sea levels. The complex consequences of this pose challenges, a shared responsibility for which we must find solutions together.
Maximizing energy efficiency to reduce both CO2 emissions and costs is crucial. We focus primarily on transport, as this is where the most significant gains can be made. The transport of plastic pallets accounts for more than 80% of the CO2 emissions in this industry.
Continuous improvement
Whether it’s about water or energy consumption, materials, CO2 emissions, or waste, our company has much to gain. Our engineers are constantly working to improve and expand our range of plastic pallets. The focus is on lightweight design, less yield loss, and the (re)use of parts and production scrap.
The innovative concepts and products are aimed at keeping our customers at the top. That's why we often design in consultation and can meet the most specific requirements with our plastic pallets. As a manufacturer and supplier, Q-Pall is even one of the market leaders in custom plastic pallets. The many advantages of our plastic pallets make this logistical tool better in almost every way.
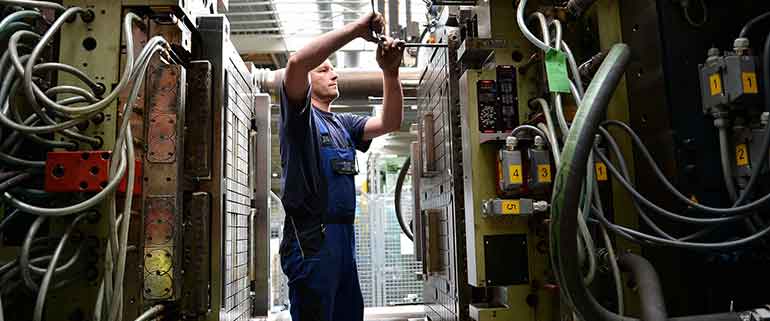
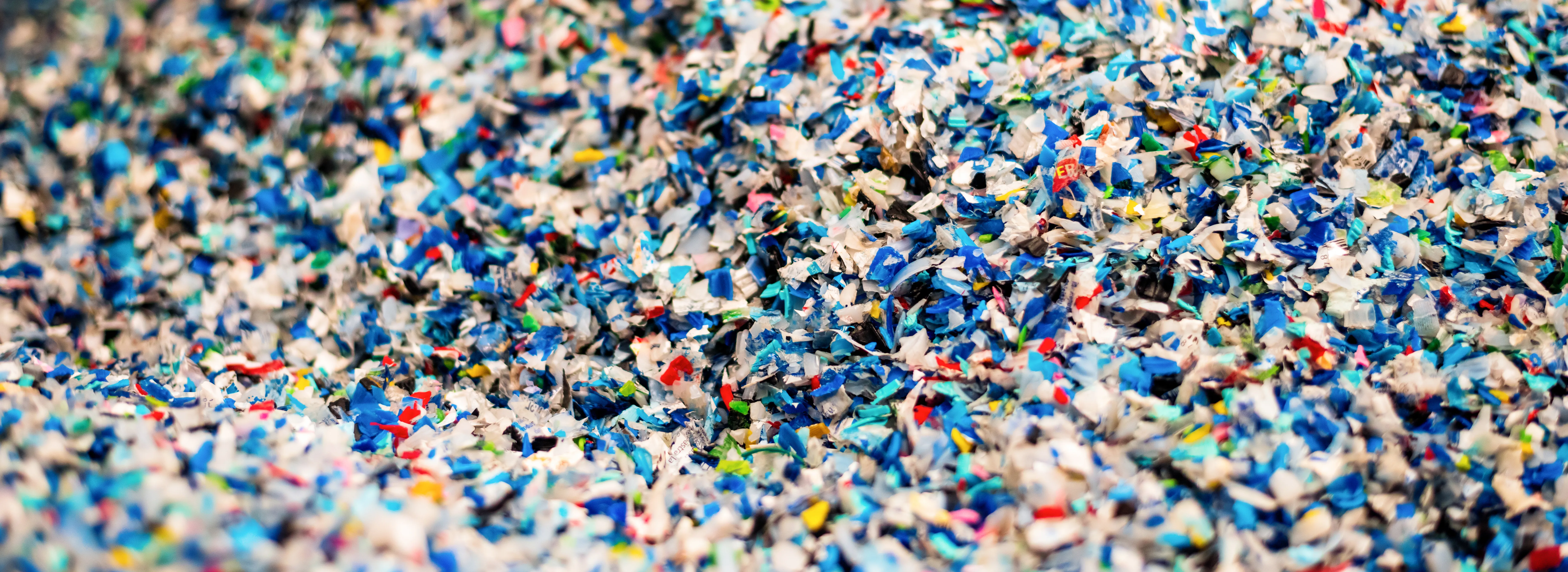
Maximize reuse
We live in a plastic era, in which more than 300 million tons of plastic are produced globally each year. Unfortunately, 5 to 15 million tons of this end up in our oceans, where the 'plastic soup' is becoming a seriously problematic issue.
Today, 98% of pallets are made from recycled material. In addition, we are committed to a better future by supporting projects that create awareness and involvement in the plastic waste problem